なぜなぜ分析とは?その基本概念と効果について徹底解説
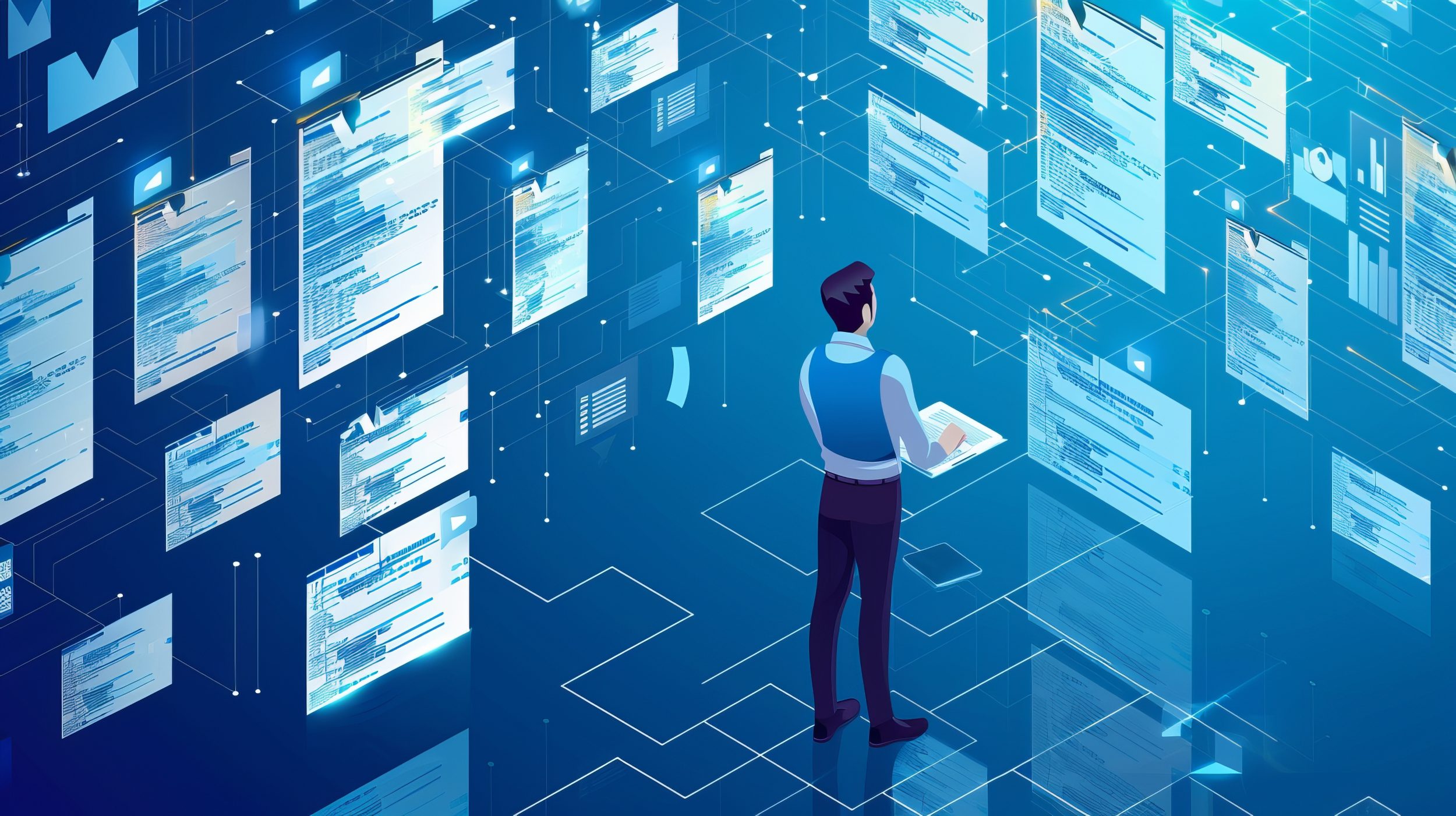
目次
- 1 なぜなぜ分析とは?その基本概念と効果について徹底解説
- 2 トヨタ生産方式とは?カイゼン活動との深い関係
- 3 自働化(Autonomation)の仕組みとメリットについて解説
- 4 ジャスト・イン・タイム(Just-in-Time)の基本原則と活用方法
- 5 7つのムダとは何か?その具体例と排除のアプローチ
- 6 なぜなぜ分析の手順と実践時のポイントと注意点
- 7 なぜなぜ分析の手順と実践時のポイントと注意点
- 8 トヨタ生産方式の基本思想とその実践方法について
- 9 カイゼン活動との関係: トヨタ生産方式を支える実践的アプローチ
- 10 ジャスト・イン・タイム(Just-in-Time)の基本原則と活用方法
- 11 自働化(Autonomation)の仕組みと実践方法の詳細
なぜなぜ分析とは?その基本概念と効果について徹底解説
なぜなぜ分析は、トヨタ自動車が発案した問題解決手法で、発生した問題の真の原因を追究することを目的としています。
この手法では、問題が発生した際に「なぜ?」を5回以上繰り返し問いかけることで、表面的な原因にとどまらず、根本的な課題を明らかにします。
これにより、単なる応急処置ではなく、再発防止につながる具体的な対策を策定できます。
特に製造業をはじめとした多くの業界で採用されており、業務プロセスの改善や品質向上に寄与しています。
この分析手法は、論理的であると同時に、現場の事実に基づいた実践的なアプローチとして評価されています。
なぜなぜ分析の概要とその発案背景について
なぜなぜ分析は、トヨタ生産方式の一環として発展しました。
この手法は、問題解決を迅速かつ効果的に行うために設計されており、現場での問題解決を重視しています。
その背景には、「問題の原因を深掘りしないまま対処することは、同じ問題の再発を招く」という考え方があります。
発案当初は主に製造業で使用されていましたが、その有用性から、サービス業やIT業界など、さまざまな分野に応用されています。
なぜなぜ分析が効果的な問題解決手法とされる理由
なぜなぜ分析が効果的とされる理由は、再発防止に焦点を当てた点にあります。
この手法では、問題の表面に現れる症状ではなく、その背後にある根本原因を特定します。
これにより、問題が繰り返し発生するのを防ぎ、長期的な視点での解決策を見出すことが可能です。
また、分析過程で現場の従業員が主体的に関与することで、現場の知識と経験を活かした解決策を導き出すことができます。
なぜなぜ分析の他の分析手法との比較
なぜなぜ分析は、他の分析手法と比較してシンプルでありながら、強力な結果をもたらします。
例えば、統計的分析やフローチャートを用いた手法に比べて、特別なツールやスキルを必要としません。
そのため、現場での即時実行が可能です。
一方で、徹底的な論理的思考が求められるため、分析者の経験と知識が結果に大きく影響します。
これがメリットでもあり、場合によっては課題ともなります。
現場でなぜなぜ分析を実施する際の注意点
なぜなぜ分析を現場で行う際には、客観性を保つことが重要です。
感情や個人の意見に左右されず、事実に基づいた議論を進める必要があります。
また、「なぜ」の問いかけが浅いレベルで終わってしまうと、真の原因を特定できず、効果的な解決策に結びつかない可能性があります。
そのため、適切なリーダーシップと明確なプロセス管理が欠かせません。
なぜなぜ分析を導入するメリットとデメリット
なぜなぜ分析を導入することで、組織全体の問題解決能力が向上します。
根本原因に基づいた対策を講じることで、業務の効率化や品質向上が期待できます。
しかし、分析が適切に行われない場合、時間やリソースの浪費につながるリスクもあります。
また、組織内で十分な理解とサポートが得られないと、分析の結果が有効活用されない可能性があります。
トヨタ生産方式とは?カイゼン活動との深い関係
トヨタ生産方式(TPS)は、トヨタ自動車が生み出した生産管理哲学で、効率性と柔軟性を重視した世界的に有名な手法です。
この方式は、ムダを排除し、生産性を最大化することを目的としています。
「自働化(Autonomation)」と「ジャスト・イン・タイム(Just-in-Time)」という2つの柱を中心に展開されており、従業員が主体的に改善活動(カイゼン)を行う文化が特徴です。
この手法は、製造業だけでなくサービス業やIT業界など、幅広い分野で応用され、その効果が広く認識されています。
トヨタ生産方式の歴史とその発展の経緯
トヨタ生産方式の歴史は、戦後の日本の経済復興期にさかのぼります。
資源の制約が厳しい中で、トヨタ自動車は効率的な生産方法を模索しました。
その結果、アメリカの大量生産方式から影響を受けつつも、日本の事情に合わせて「少量多品種生産」に適応する形でTPSを発展させました。
この方式は、1950年代に大野耐一氏によって体系化され、トヨタの競争力の礎となりました。
その後、グローバル化の進展とともに、TPSは世界中で評価され、他社にも取り入れられるようになりました。
カイゼン活動がトヨタ生産方式における役割
カイゼン活動は、トヨタ生産方式において重要な要素の一つです。
現場の従業員が主体的に問題を見つけ、解決策を提案するプロセスが、組織全体の生産性向上につながります。
カイゼン活動では、「現場主義」が重視され、実際の作業現場での観察と実践が鍵となります。
この活動を通じて、従業員のスキル向上やチームワークの強化が図られ、企業全体の競争力が高まります。
トヨタ生産方式の特徴とその実践の要点
トヨタ生産方式の特徴は、ムダの徹底的な排除と柔軟な生産体制です。
「自働化」による品質管理と、「ジャスト・イン・タイム」による在庫の最小化がその核心です。
この方式では、生産ライン全体の連携が重視され、各工程での問題発見と迅速な対応が求められます。
また、標準作業や継続的な改善が組織文化として根付いており、これがTPSの持続的な成功の鍵となっています。
他業界におけるトヨタ生産方式の応用例
トヨタ生産方式は、製造業以外の業界でも幅広く応用されています。
例えば、サービス業では顧客満足度向上のための業務改善に活用され、IT業界ではアジャイル開発との親和性が高いとされています。
また、医療業界では、患者の待ち時間削減や業務プロセスの効率化に寄与しています。
これにより、TPSはさまざまな業界での成功事例を生み出し、グローバルな影響力を持つ手法として確立されています。
トヨタ生産方式の成功事例とその効果
トヨタ生産方式の成功事例として、トヨタ自動車の高い生産効率と品質が挙げられます。
この方式を採用することで、トヨタは短期間での新車投入や競争力のある価格設定を可能にしました。
また、他の企業でもTPSを導入することで、生産コスト削減や製品品質の向上を達成した事例が報告されています。
これらの成功事例は、TPSがただの生産管理手法ではなく、持続的な競争優位を築くための戦略であることを証明しています。
自働化(Autonomation)の仕組みとメリットについて解説
自働化(Autonomation)は、トヨタ生産方式の柱の一つであり、機械や設備に人間の知恵を加えることで、異常が発生した際に自動的に生産を停止させる仕組みを指します。
この概念は、品質管理と効率的な生産の両立を目指して開発されました。
自働化の目的は、不良品の発生を防ぎ、問題が大きくなる前に迅速に対処することです。
この仕組みにより、人員の負担軽減と生産効率の向上が実現され、トヨタの競争力を支える重要な要素となっています。
自働化とは?その定義と基本的な機能
自働化は「自動化」と似ていますが、重要な違いは「異常検知と停止機能」が加わっている点です。
単なる機械の自動操作ではなく、製品やプロセスに問題が発生した場合、即座に検知して生産を停止する仕組みが含まれます。
これにより、不良品が大量に生産されることを防ぎ、品質管理を強化できます。
例えば、部品が正しくセットされていない場合や異常な音や振動が発生した場合に機械が停止することで、問題の早期発見と迅速な対処が可能となります。
自働化がトヨタ生産方式における重要性
自働化は、トヨタ生産方式において不可欠な要素です。
この仕組みにより、生産ライン全体の品質が向上し、効率的な運用が可能となります。
特に、異常が発生した場合に迅速に対応することで、工程全体の停滞を防ぎます。
また、従業員は異常対応に専念できるため、作業負荷が軽減されます。
このように、自働化は品質管理と効率性の両面で重要な役割を果たしており、トヨタの高い生産性を支える基盤となっています。
自働化による生産効率の向上と不良品削減の効果
自働化は、生産効率の向上に大きく貢献します。
例えば、異常が検知されると自動的にラインが停止するため、大量の不良品が生産される事態を防ぎます。
また、問題の発見と修正が迅速に行われるため、ダウンタイムの短縮にも寄与します。
さらに、従業員が不良品の処理に時間を割く必要がなくなり、より付加価値の高い業務に集中できるようになります。
結果として、企業全体の生産性が向上し、競争力の強化につながります。
自働化の導入事例と成功の秘訣
自働化の成功事例として、多くの自動車メーカーがトヨタの手法を参考にし、生産効率と品質を大幅に向上させた事例があります。
例えば、トヨタの海外工場では、自働化により不良率が大幅に減少し、コスト削減が実現されました。
成功の秘訣は、現場の状況に適した技術を選定し、従業員がその仕組みを理解し活用できるよう教育を徹底することにあります。
また、継続的な改善活動を通じて、自働化の効果を最大限引き出す取り組みが行われています。
自働化の課題とその解決策
自働化の導入には、いくつかの課題も存在します。
まず、初期投資が高額である点が挙げられます。
また、システムの設計や運用が不十分な場合、期待する効果が得られないことがあります。
これらの課題を解決するためには、徹底した現場調査と適切な設備投資が必要です。
さらに、従業員のトレーニングを通じて、新しい仕組みに慣れてもらうことが重要です。
これにより、自働化のメリットを最大限に享受することができます。
ジャスト・イン・タイム(Just-in-Time)の基本原則と活用方法
ジャスト・イン・タイム(Just-in-Time、JIT)は、トヨタ生産方式のもう一つの柱であり、「必要なものを、必要なときに、必要な量だけ」供給するという基本原則に基づいています。
この手法は、在庫を最小化し、効率的な生産プロセスを実現するための重要な考え方です。
JITの目的は、ムダを排除し、生産の柔軟性と効率性を向上させることにあります。
この手法は、製造業に限らず、さまざまな業界で活用されています。
ジャスト・イン・タイムの基本理念と背景
ジャスト・イン・タイムは、戦後の資源不足の時代にトヨタが生み出した手法です。
この考え方は、必要な在庫を最小限に抑え、余剰や浪費を徹底的に排除することを目指しています。
背景には、限られた資源を効率的に活用するという経済的なニーズがありました。
この手法が導入された結果、トヨタは無駄を省きながら、需要に柔軟に対応する生産体制を構築することができました。
ジャスト・イン・タイムが在庫管理に与える影響
ジャスト・イン・タイムの導入により、在庫管理の効率が飛躍的に向上します。
余分な在庫を抱えるリスクが減少し、資金効率が向上します。
また、在庫スペースが削減されることで、コスト削減につながります。
一方で、需要の変動に迅速に対応するためには、サプライヤーとの密接な連携が必要です。
これにより、サプライチェーン全体が一体となって効率化を図ることが可能となります。
7つのムダとは何か?その具体例と排除のアプローチ
7つのムダは、トヨタ生産方式の核心概念の一つで、生産効率を向上させるために排除すべき非効率な要素を指します。
この概念は、現場におけるプロセス改善の指針として広く利用されています。
具体的には、「加工のムダ」「在庫のムダ」「不良や手直しのムダ」「手待ちのムダ」「作りすぎのムダ」「動作のムダ」「運搬のムダ」の7つに分類されます。
それぞれが生産活動におけるコスト増加や品質低下の原因となるため、これらを見つけ出し、改善することがトヨタ生産方式の基本的なアプローチです。
7つのムダの定義とそれぞれの特徴について
7つのムダは、各プロセスにおける非効率な活動を具体的に定義したものです。
「加工のムダ」は、製品に付加価値を生まない余計な作業、「在庫のムダ」は、不要な在庫の維持によるコスト増加、「不良や手直しのムダ」は、品質問題による再作業や廃棄物の発生を指します。
「手待ちのムダ」は、作業員や機械が非稼働状態にある時間、「作りすぎのムダ」は需要を超えた生産による在庫の積み上がり、「動作のムダ」は不要な動きや移動、「運搬のムダ」は製品や材料の不要な移動を指します。
これらの特徴を理解することが、効果的な改善の第一歩です。
加工のムダの具体例と改善方法
加工のムダの典型例として、不要な工程や過剰品質を追求する作業が挙げられます。
例えば、必要以上の研磨や塗装は、時間と資源の浪費につながります。
このムダを排除するには、各工程の価値を明確にし、不要な作業を削減することが必要です。
具体的には、プロセスの標準化や自動化を活用することで、工程全体の効率を向上させることが可能です。
また、従業員からのフィードバックを取り入れることで、現場に即した改善が期待できます。
在庫のムダの発生原因とその削減策
在庫のムダは、生産プロセスの過剰供給や需要予測の誤りによって発生します。
これにより、資金繰りの悪化や保管コストの増加といった問題が生じます。
このムダを削減するためには、ジャスト・イン・タイム(Just-in-Time)を実践し、需要に応じた生産を徹底することが重要です。
また、在庫管理システムの導入により、リアルタイムでの在庫状況の把握が可能となり、過剰在庫を防ぐことができます。
不良や手直しのムダを減らすための取り組み
不良品や手直しの発生は、品質管理の不備が原因であることが多いです。
このムダを減らすためには、プロセスの標準化や従業員のスキル向上が重要です。
例えば、自働化(Autonomation)の導入により、異常が発生した際に即座に生産を停止させる仕組みを構築することで、不良品の流出を防ぐことができます。
また、PDCA(計画・実行・評価・改善)サイクルを回すことで、継続的な改善を図ることが可能です。
7つのムダを排除するための実践的なツールと方法
7つのムダを効果的に排除するには、5S活動(整理・整頓・清掃・清潔・しつけ)やカイゼン活動を活用することが有効です。
また、現場のムダを可視化するためのバリューストリームマッピング(VSM)や、ボトルネックを特定するための理論的手法である制約理論(TOC)も役立ちます。
これらのツールを駆使して、全体的なプロセスの効率化を図ることで、7つのムダを根本から削減することが可能です。
なぜなぜ分析の手順と実践時のポイントと注意点
なぜなぜ分析は、問題解決において非常に重要な手法であり、「なぜ?」を繰り返すことで問題の真因を追究します。
この手法を適切に実施することで、単なる応急処置ではなく、再発防止に向けた根本的な対策が可能になります。
しかし、効果を発揮するためには、正しい手順と注意点を理解することが必要です。
本節では、具体的な手順や注意点を解説し、なぜなぜ分析を成功させるためのポイントを探ります。
なぜなぜ分析の実施手順とそのプロセス
なぜなぜ分析の基本的な手順は、問題を定義し、「なぜ?」を5回以上繰り返すことです。
例えば、「製品の不良が発生した」という問題に対して、「なぜ不良が発生したのか?」を問い、その回答に対してさらに「なぜ?」を繰り返します。
これにより、表面的な原因から根本原因へと辿り着きます。
このプロセスでは、問題が発生した現場でのデータや観察結果を活用し、客観的な視点で分析を行うことが重要です。
なぜを5回以上繰り返すことで真因を追究する方法
「なぜ」を5回以上繰り返すことは、問題解決の本質に迫るための効果的な手法です。
この方法では、表面的な要因を深掘りし、真因を明らかにします。
ただし、適切に繰り返さなければ、単なる思いつきや感情的な結論に終わる可能性があります。
そのため、各「なぜ」に対する回答は、事実に基づいて論理的に導き出されるべきです。
また、関係者全員の合意を得ながら進めることで、分析結果の信頼性を高めることができます。
なぜなぜ分析の手順と実践時のポイントと注意点
なぜなぜ分析は、トヨタ生産方式の中核を成す手法の一つで、問題解決のための根本原因を追究するプロセスです。
この手法の最大の強みは、単なる表面的な問題解決にとどまらず、問題の再発防止に寄与する点です。
「なぜ」を5回以上繰り返すことで、表面の原因からさらに深い本質的な原因に到達します。
しかし、効果的に実施するには適切な手順や注意点を理解し、実行することが求められます。
以下では、具体的な手順や成功のためのポイントを詳しく解説します。
なぜなぜ分析の実施手順とそのプロセス
なぜなぜ分析の基本的な手順は以下の通りです。
まず、問題の定義を明確にし、分析の対象を具体的に特定します。
次に、その問題に対して「なぜ?」を繰り返し問いかけ、原因を掘り下げていきます。
例えば、製品の不良が発生した場合、「なぜ不良が発生したのか?」から始め、回答に対してさらに「なぜ?」を繰り返します。
このプロセスでは、データや現場観察に基づいた事実を重視することが重要です。
最後に、見つかった根本原因に基づいて、具体的で実行可能な対策を策定します。
なぜを5回以上繰り返すことで真因を追究する方法
「なぜ」を5回以上繰り返すことで、問題の真因を徹底的に探ることができます。
この手法は、単なる推測ではなく、事実に基づく分析を重視します。
例えば、「機械が停止した」という問題に対して、「なぜ機械が停止したのか?」という問いに始まり、「電源が落ちたから」「なぜ電源が落ちたのか?」「配線が緩んでいたから」というように繰り返し問いかけます。
このプロセスを通じて、根本原因を明確にし、対策の精度を高めることができます。
ただし、適切な問いの設定と事実確認を怠ると、誤った結論に至る可能性があるため注意が必要です。
なぜなぜ分析を成功させるためのチームの役割
なぜなぜ分析は、チーム全体で取り組むことで最大の効果を発揮します。
現場の従業員や関係者を含めた多様な視点を持つメンバーが参加することで、より広範囲の原因を見つけることが可能です。
チーム内での役割分担も重要で、議論をリードするファシリテーターや、事実確認を担当するメンバーを明確にします。
また、メンバー間の信頼関係を構築し、自由な意見交換ができる環境を整えることで、分析の精度が向上します。
なぜなぜ分析で失敗しやすいケースとその回避方法
なぜなぜ分析の失敗例として、原因を早急に特定しようとすることで真因に辿り着けないケースがあります。
また、個人や特定の部署に原因を押し付けることで、正確な分析が妨げられることもあります。
これを防ぐためには、感情的な判断を排除し、事実に基づいて冷静に分析を進めることが必要です。
また、「なぜ?」を深掘りする際には、すべての問いに論理的な裏付けを求め、データを活用することが重要です。
なぜなぜ分析を最大限活用するためのアプローチ
なぜなぜ分析を効果的に活用するには、現場での実践と定期的な見直しが不可欠です。
分析結果を組織全体で共有し、類似の問題が他の現場で発生しないように対策を展開することが重要です。
また、分析を行った後も、その結果を評価し、必要に応じて改善を繰り返すことで、継続的な効果を得ることができます。
さらに、社員教育を通じて、なぜなぜ分析の重要性を全社的に理解させることも、成功の鍵となります。
トヨタ生産方式の基本思想とその実践方法について
トヨタ生産方式(TPS)の基本思想は、「自働化」と「ジャスト・イン・タイム(Just-in-Time)」を主軸とし、ムダを徹底的に排除することで生産効率を最大化する点にあります。
この哲学は、現場での継続的な改善(カイゼン)活動を促進し、全体的な生産プロセスの合理化を実現します。
TPSは製造業界で革新的な成功を収めただけでなく、他の業界にも広がりを見せており、現在では効率性と持続可能性を追求する企業の指針となっています。
自働化とジャスト・イン・タイムの基本的な違いと役割
自働化は、機械が異常を検知した際に自動で生産を停止する仕組みを意味し、品質管理に焦点を当てています。
一方、ジャスト・イン・タイムは、必要なものを必要なときに必要なだけ供給することにより、生産効率を向上させます。
両者は、トヨタ生産方式の中で相互に補完し合い、生産性と品質を同時に向上させる役割を果たしています。
これらの概念は、従業員の働き方にも影響を与え、問題解決と効率的な運用を促進します。
ムダの徹底排除が生産効率に与える影響
TPSの中心思想であるムダの排除は、生産効率を高める上で重要な役割を果たします。
ムダには、在庫、動作、不良などの7つの要素が含まれており、これらを最小限に抑えることで、生産プロセスの無駄な時間やコストを削減できます。
また、ムダの排除は、効率化だけでなく、従業員の働きやすさや顧客満足度の向上にも寄与します。
具体的な例として、現場の作業効率を改善することで、納期遵守率が向上するケースが多く見られます。
カイゼン活動との密接な関係性
TPSにおけるカイゼン活動は、従業員が自発的に問題を特定し、改善策を提案する仕組みです。
この活動は、現場の効率化や従業員のスキル向上に直接的な影響を与えます。
例えば、作業手順の見直しや新しいツールの導入によって、短期間で大きな改善を実現することが可能です。
カイゼン活動がTPSに不可欠な理由は、現場での柔軟性を確保し、長期的な競争力を維持する点にあります。
他業界におけるトヨタ生産方式の応用事例
TPSの応用事例は製造業に限らず、多くの業界で成功を収めています。
例えば、IT業界では、TPSの考え方がアジャイル開発やリーンスタートアップに影響を与えています。
また、医療業界では、患者の待ち時間を削減するためにTPSの原則が採用されるケースもあります。
このような事例は、TPSが業界を問わず、効率性と品質を高める手法として有効であることを示しています。
トヨタ生産方式を現場で実践する際の重要なポイント
TPSを現場で実践するためには、全従業員がその思想を理解し、積極的に参加することが重要です。
具体的には、現場主義を徹底し、データに基づいた意思決定を行うことが求められます。
また、問題が発生した際には迅速に対応し、根本的な解決策を見つけるプロセスが必要です。
さらに、経営層から現場までが一体となって改善活動を推進することで、TPSの効果を最大限引き出すことが可能となります。
カイゼン活動との関係: トヨタ生産方式を支える実践的アプローチ
カイゼン活動は、トヨタ生産方式を実践する上で欠かせない要素です。
この活動は、現場の作業者が自発的にプロセス改善を行う仕組みであり、組織全体の競争力向上に寄与します。
特に、継続的な改善を重視するカイゼン活動は、TPSの「現場主義」思想と深く結びついています。
以下では、カイゼン活動の基本的な考え方とその実践例、成功のためのポイントを詳しく解説します。
カイゼン活動の概要と基本的な考え方
カイゼン活動は、日本語で「改善」を意味し、小さな改善を積み重ねることで大きな効果を生むことを目的としています。
この活動では、現場での観察やデータ分析を基に、具体的な改善案を提案し、実行に移します。
また、全員参加型のアプローチを採用しており、経営陣から現場作業員までが一体となって取り組む点が特徴です。
このように、カイゼン活動は、効率的な運用と継続的な成長を支える原動力となっています。
カイゼン活動が生産効率に与える影響
カイゼン活動は、生産効率を大幅に向上させる可能性を秘めています。
例えば、作業の無駄を削減することで、プロセス全体の時間短縮やコスト削減が期待できます。
また、従業員が主体的に改善案を提案することで、現場でのモチベーションが向上し、組織全体の士気も高まります。
これにより、単なる効率化にとどまらず、従業員の成長や組織文化の改善にも寄与します。
ジャスト・イン・タイム(Just-in-Time)の基本原則と活用方法
ジャスト・イン・タイム(JIT)は、トヨタ生産方式の柱となる考え方で、「必要なものを、必要なときに、必要な量だけ」生産するという原則に基づいています。
この手法は、生産プロセス全体を効率化し、ムダを最小限に抑えることを目的としています。
特に、在庫コストの削減や納期の短縮に大きな効果を発揮します。
JITは、トヨタの成功を支える重要な要素であり、製造業だけでなく、サービス業やIT業界などでも応用されています。
ジャスト・イン・タイムの基本理念と背景
JITの基本理念は、ムダの徹底的な排除にあります。
この考え方は、戦後の日本における資源不足の中で、効率的な生産方法を模索した結果として生まれました。
特に、トヨタの工場では、余分な在庫を持つリスクを減らし、生産ラインの柔軟性を高めるためにJITが導入されました。
その背景には、「在庫は必要なものだけを持つ」という徹底した効率化の哲学があり、これがトヨタの競争力の基盤となりました。
ジャスト・イン・タイムが在庫管理に与える影響
JITの導入によって、在庫管理の効率が飛躍的に向上します。
具体的には、余剰在庫を抱える必要がなくなるため、在庫スペースや保管コストが削減されます。
また、需要に応じた生産が可能となるため、在庫切れや余剰在庫のリスクが減少します。
この仕組みは、サプライチェーン全体の連携を強化し、供給の安定性を確保する上でも重要です。
結果として、資金効率が向上し、企業全体の経済的なメリットが得られます。
ジャスト・イン・タイムの導入ステップと具体的手法
JITを導入するには、いくつかのステップがあります。
まず、現場での生産プロセスを詳細に分析し、ムダを特定します。
次に、需要予測を基に、適切な生産計画を立てます。
また、サプライヤーとの緊密な連携を構築し、必要な部品や資材を適時に供給できる体制を整えます。
さらに、生産ラインを柔軟に運用するために、標準作業や多能工の育成を進めます。
これらの手法を組み合わせることで、JITの効果を最大限に引き出すことが可能です。
ジャスト・イン・タイムがもたらす経済的メリット
JITの最大のメリットは、経済的な効果にあります。
在庫削減によるコスト節約はもちろん、迅速な納品が可能になることで顧客満足度が向上します。
また、生産ラインの柔軟性が高まるため、需要の変動に迅速に対応できます。
これにより、企業は競争力を強化し、市場での優位性を確立することができます。
さらに、余剰在庫を抱えるリスクが減少するため、資金効率が向上し、収益性の向上にも寄与します。
ジャスト・イン・タイムの運用上の注意点
JITの運用には、いくつかの課題もあります。
例えば、需要の急激な変化に対応できない場合、供給不足が発生する可能性があります。
また、サプライヤーとの連携が不十分な場合、部品供給が滞るリスクがあります。
これを防ぐためには、需要予測の精度を高めるとともに、サプライヤーとの密接なコミュニケーションを維持することが重要です。
さらに、リスク管理の一環として、必要最小限の安全在庫を確保することも有効な対策です。
自働化(Autonomation)の仕組みと実践方法の詳細
自働化は、トヨタ生産方式における品質管理の要であり、機械に人間の知恵を加えることで異常を検知し、自動的に生産を停止させる仕組みです。
この手法は、不良品の大量生産を防ぎ、問題が発生した際に迅速に対応することを可能にします。
また、自働化の導入により、従業員がより付加価値の高い作業に集中できる環境が整います。
以下では、自働化の具体的な仕組みやメリット、導入のためのステップについて詳しく解説します。
自働化の基本的な考え方とその定義
自働化は、単なる自動化とは異なり、「異常が発生したら自動で生産を停止する」という知的な機能が含まれています。
この仕組みにより、品質管理が強化され、不良品が次の工程に進むのを防ぎます。
例えば、センサーを活用して異常を検知し、機械を停止させることが一般的です。
このような自働化の仕組みは、トヨタの生産現場での品質向上に大きく寄与しています。
自働化が生産現場に与えるメリット
自働化の導入により、品質の向上だけでなく、生産効率の向上やコスト削減も期待できます。
例えば、異常が発生した際に即座に対応できるため、ダウンタイムを最小限に抑えることが可能です。
また、不良品が発生するリスクが減少することで、材料費や手直しコストの削減にもつながります。
さらに、従業員が異常対応に時間を割かずに済むため、より創造的な業務に専念できる環境が整います。